Como avaliar e exprimir a eficácia de um meio produtivo?
Desde o início da era industrial que uma das principais preocupações de qualquer Gestão de uma unidade produtiva tem sido: como avaliar e exprimir corretamente a eficácia dos seus meios produtivos. Ao longo do século XX foram ensaiadas diversas soluções, mas não se conseguia estabelecer um critério comum, pelo que, quando se tratava de comparar entre si a eficácia de meios produtivos entre unidades industriais, invariavelmente acabavam por se comparar números que exprimiam coisas diferentes. Eram (e ainda são) comuns indicadores de natureza predominantemente financeira, eram (e também ainda são) comuns indicadores de natureza de pura gestão de produção.
É forçoso reconhecer que existem indicadores de ambas as naturezas que são muito úteis, mas infelizmente apenas exprimem aspetos particulares do contexto produtivo além do que muitos deles são vulneráveis a diferenças de interpretação por parte dos seus utilizadores, conduzindo a resultados falsos ou pelo menos enviesados segundo as conveniências dos utilizadores.
É frequente constatar-se a publicação de indicadores otimistas de performance que não traduzem minimamente a situação real de um aparelho produtivo.
A alternativa do OEE
São numerosos os autores que atribuem a Seiichi Nakajima (anos 60) a criação formal do OEE (Overall Equipment Effectiveness) como meio de cálculo e de forma de expressão da eficácia da utilização de um meio produtivo. O OEE é hoje reconhecido como um dos melhores e mais completos indicadores de medição da eficácia de um sistema. Mas, tal como qualquer indicador, requer a existência de um sistema de recolha e tratamento de informação:
- Base de dados de fabrico atualizada – pelo menos de gamas ou routings de fabrico completos e atualizados e ciclos de fabrico exatos;
- Existência de um sistema de gestão da Manutenção e dados consistentes e fiáveis sobre tempos de utilização de equipamentos e seus tempos de paragem;
- Sistema fiável de controlo e quantificação – em quantidade em valor, da não qualidade gerada nos processos.
O OEE é um indicador composto, que tenta quantificar o resultado da interação de três outros indicadores calculados separadamente como forma de traduzir a eficácia de operação de um equipamento: a performance, a disponibilidade e a qualidade.
A performance
(P – sob a forma de uma percentagem)
A Performance do equipamento tenta quantificar a forma real de como esse equipamento é utilizado. A sua determinação foca-se no tempo efetivo de utilização eficaz, expurgando-o de todas as situações de subutilização - independentemente de serem justificáveis ou não, e compara-o com o tempo durante o qual, esse mesmo equipamento esteve apto para produzir. Por outras palavras, o equipamento “estava apto” e durante todo esse tempo em que esteve apto, se tivesse trabalhado em condições normais de utilização, deveria ter produzido uma determinada quantidade de produção.
Se não o fez, então houve um desperdício de recursos. A Performance, quantifica esse “desperdício” de capacidade e de recursos produtivos.
A determinação da Performance pode fazer-se de uma forma sintética (um equipamento específico) ou de uma forma alargada (um grupo), conforme âmbito da análise que se pretende.
Um meio produtivo é um sistema onde entram recursos (matérias primas, mão de obra, tempo de maquinação, etc.) e saem produtos acabados destinados ao mercado. A participação de cada um dos recursos introduzidos num produto é (deverá ser) rigidamente regida através da base de dados de produção: as nomenclaturas dos produtos, os routings de fabrico, o ficheiro dos postos de carga, e outros. Estes dados interagem entre si, determinando o Tempo de Ciclo de cada uma das operações de cada produto ou do produto completo.
Na sua forma mais simples, o cálculo da performance recorre justamente ao tempo de ciclo ideal estabelecido para cada produto.
O cálculo é simples: no final de um determinado período (um mês, por exemplo), um equipamento produziu uma determinada quantidade de artigos que foram aprovados e que, ou foram vendidos, ou aguardam venda no armazém de produto acabado. Multiplicando essa quantidade de artigos pelo tempo ideal de ciclo, obtém-se um tempo – o tempo do seu funcionamento que a máquina conseguiu converter efetivamente em produtos. Esse tempo “eficaz” é necessariamente menor que o tempo em que a máquina esteve disponível para produzir (tempo de afetação à atividade produtiva) já que houve paragens diversas (mudanças, afinações, etc.) bem como possíveis tempos de não utilização (por exemplo, falta de carga). O equipamento esteve parado por falta de carga? É lamentável, mas o certo é que o equipamento poderia ter produzido e não produziu, logo o equipamento foi subutilizado. O tempo utilizado para cálculo do tempo de aptidão para produzir depende obviamente do regime de funcionamento da unidade fabril (8 horas/dia, 16 horas/dia, etc.) e do número de dias de funcionamento.
Sinteticamente, um meio produtivo pode considerar-se uma máquina onde entra um porco e saem salsichas. Se a máquina for reversível, então introduzindo todas as salsichas produzidas num determinado período, deverá sair um porco inteiro. Mas nunca sai um porco inteiro. Falta sempre pelo menos uma pata, quando não falta muito mais.
Aquilo que falta do porco é muito simplesmente todo o input que o sistema não conseguiu transformar em output. As razões poderão ser as mais diversas, desde causas perfeitamente justificadas até improdutividade pura e simples, mas o fato inquestionável é que apenas uma percentagem dos recursos consumidos pelo sistema foram transformados em produto acabado, logo, em receita.
Assim, a eficácia de utilização de uma máquina obtém-se comparando o tempo que teoricamente teria sido necessário para produzir os produtos acabados concluídos, com o tempo (necessariamente maior) de disponibilidade (alternativamente, o tempo de afetação) dessa máquina.
Questão: deve usar-se o Tempo de Aptidão para fabrico ou tempo de Afetação?
Trata-se de um ponto que não consegue reunir consenso dos teóricos. Uns argumentam que os tempos sem carga deverão ser excluídos do indicador; outros opinam que poderá ser lamentável não haver carga, mas o fato é que a máquina poderia ter produzido e não produziu; logo, o tempo a considerar é todo o tempo durante o qual a máquina esteve apta para produzir.
Os valores “normais” da performance variam muito com a natureza da atividade fabril em questão, mas será desejável que sejam superiores a 80% mesmo nos casos mais desfavoráveis. Bem vistas as coisas, uma performance de 80% significa que a empresa não consegue transformar em produto acabado, 20% de todo o seu input.
Disponibilidade
(D – sob a forma de uma percentagem)
A Disponibilidade de um meio (ou conjunto integrado de meios produtivos) tenta quantificar a qualidade da manutenção de que esse(s) meio(s) beneficia(m) e em que medida condicionam a sua aptidão para produzir. Trata-se de um indicador standard utilizado por muitos departamentos de manutenção para avaliar a eficácia do respetivo sistema.
A disponibilidade (em %) é dada por:
MTBF = (Mean Time Between Failures - Tempo médio entre avarias, expresso em horas): exprime o tempo médio que mediará entre duas avarias consecutivas de um mesmo equipamento. Obviamente que quanto maior for o tempo entre duas avarias consecutivas, mais fiável será o equipamento subentendendo-se que essa fiabilidade é uma consequência da qualidade de Manutenção de que beneficia.
MTTR = (Mean Time To Repair – Tempo médio para reparar, expresso em horas): exprime o tempo que em média requerem as reparações desse equipamento, eventualmente expurgado dos tempos de espera (ex. º tempo entre a comunicação do estado de avaria, tempo de espera por componentes para proceder à reparação, etc.). Quanto menor for o tempo médio requerido pelas reparações (ou aguardando reparação):
- Mais eficaz será o serviço de manutenção;
- Menos importantes / mais simples serão as avarias de que o equipamento enferma.
MWT = (Mean Waiting Time - Tempo médio de espera, expresso em horas): exprime o tempo médio de espera (o equipamento não está apto, mas também não está a ser reparado). Nota: existem autores que incorporam os tempos de espera nos tempos de reparação aparecendo assim um “novo MTTR”.
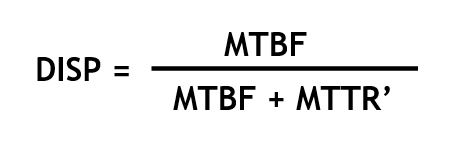
O MWT tenta exprimir:
- A influência dos fatores (através dos respetivos tempos) que intervêm na aquisição de componentes necessários à reparação de compras, sendo que esses fatores vão desde a estratégia de decisão dos componentes, mas máquinas a ter em stock, até à eficácia do Departamento de Compras;
- A influência do sistema de comunicação interno da empresa, não é raro encontrar-se MWT’s elevados unicamente por causa de uma deficiente comunicação entre Produção e Manutenção.
Há quem tente simplificar o cálculo calculando o quociente entre o número de horas efetivamente trabalhadas pelo equipamento (portanto isentas de paragem) e os tempos de afetação.
Do anteriormente exposto deduz-se que o indicador Disponibilidade, exprime numericamente a percentagem média do tempo físico possível (de acordo com calendário e regime de operação da empresa) durante a qual o equipamento está apto a trabalhar, independentemente de ser efectivamente utilizado ou não.C
omo é obvio, o MTBF é sempre inferior a 100% (disponibilidade total, sem quaisquer avarias); normalmente são consideradas disponibilidades desejáveis as que têm valores acima dos 90%.
Qualidade
(Q – sob a forma de uma percentagem)
Mas nem todos os produtos produzidos por um sistema ou por meio de fabrico estão conformes. Há produtos não conformes, rejeitados, classificados como segunda escolha, enfim, apenas uma parte da totalidade dos produtos que saem de um sistema estão aptos para venda. Embora variando com o rigor com que é determinado, é sensivelmente coincidente com o complementar da não qualidade do produto (supondo que é feito o seu cálculo individualizado).Assim, se a não qualidade de uma família de produtos for de 5%, o seu indicador de qualidade a utilizar para efeito do cálculo do OEE será 95%. Relativamente à maioria dos produtos não são aceitáveis indicadores de qualidade inferiores a 95%.
Determinação e valores de referência do OEE
Exemplificando: Na empresa XPTO obtiveram-se os seguintes rácios:
- Performance = 80%;
- Rácio de Qualidade = 95%;
- Disponibilidade = 90%.
OEE = 0,80 x 0,95 x 0,90 = 68,4%
Valores standard do OEE
Parece existir consenso em que uma empresa “World Class” apresente OEE’s superiores a 85%. Os valores de referência típicos para os indicadores parciais são de 90% para a Disponibilidade, 95% para a Performance e 99% para a Qualidade.
Todavia, são muitas as empresas de prestígio que possuem OEE’s da faixa dos 60% ou pouco mais. Na verdade, os OEE’s da maioria das empresas situam-se justamente nessa faixa dos 60-70%.
"O OEE não deve ser encarado como um fim em si próprio, mas como um meio de melhorar.
Fez uma primeira estimativa do OEE da sua empresa e encontrou 45% ou 40%? Menos? É normal. O primeiro conselho é não se fixar no número em si próprio, mas na sua capacidade de melhorar. Fixe o OEE obtido como ponto de partida. Tem vários processos? Qual deles está pior? Estabeleça prioridades. Fixe objectivos para os indicadores parciais. Ponha a sua equipa a trabalhar.
Lembre-se:
- Agora possui um indicador comparável com outras empresas e, tratando-se de um indicador “composto”, é menos sensível a manipulações e enviesamentos mais ou menos “convenientes” do ponto de vista de resultados. Meça sempre usando os mesmos referenciais; não altere critérios entre medições.
- Agora possui “números” de referência, - o melhor benchmarking que pode existir: primeiramente levar o OEE do seu sistema até à faixa “mediana” dos 60 a 70%. Depois, apostar na melhoria continua do seu sistema.
- O “seu indicador” pode ajudá-lo a definir prioridades. Qual dos três indicadores parciais é que está pior?
Note que o indicador “Performance” é muito sensível a:
- Desatualizações da base de dados;
- Situações de funcionamento degradado (abaixo dos standards);
- Faltas de registo de dados;
- Tarefas que só acrescentam custo sem acrescentar valor – que normalmente não fazem parte dos routings de fabrico, mas consomem recursos.
Considerações Finais
Para melhorarmos o OEE é essencial que toda a equipa saiba o que está a acontecer na fábrica e em tempo real. Se a sua empresa ainda não utiliza o OEE, ou se o calcula de forma manual, conheça o sistema aPROD que vai deixar a sua fábrica totalmente online, fornece o OEE de forma automática e apresenta várias informações sobre a sua produção de forma precisa, confiável e em tempo real.
Mais informação?